
操作人正確判斷拉刀的狀態(tài)方法:操作人應隨時觀察拉伸刀的切削狀態(tài),如果出現(xiàn)異常情況,則應立即排除故障,或將拉伸刀送入重磨,以免損壞拉伸刀,保證拉伸刀的正常拉伸。當拉刀變鈍時,拉削表面的光潔度會逐漸變差。在拉削過程中,拉床壓力表上顯示的壓力持續(xù)升高,則是拉刀鈍化、磨鈍程度增大的明顯標志。用尖銳的拉刀拉削時,切屑厚度均勻,邊緣平整,切屑卷曲好。當拉削產生的是切屑的斷裂和破碎,當邊緣很不平時,則表示拉刀磨鈍。拉刀齒有明顯的缺陷,如前刀面附著大塊屑瘤,切刀齒出現(xiàn)燒痕、燒傷、寬磨帶等,說明拉刀需要重磨。
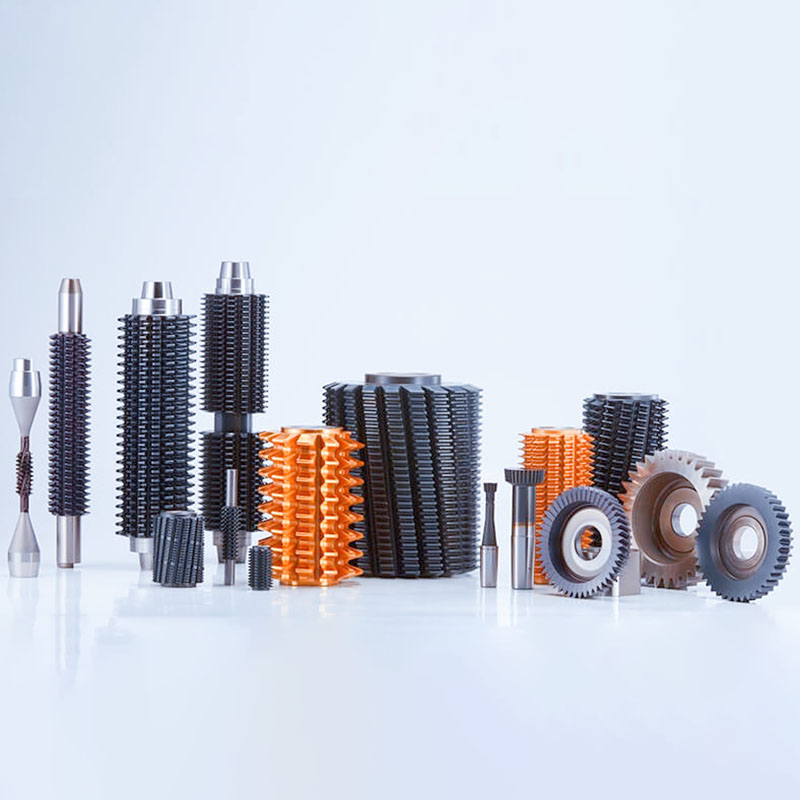
消除表面缺陷:拉削時表面產生鱗刺、縱向劃痕、壓痕、擠光、環(huán)形坡紋和啃刀等是影響拉削表面質量的常見缺陷,其形成原因很多,其中主要有:刃口鈍化或微小崩刃、刃口粘屑,刀齒刃帶過寬或寬度不均、前角太大或太小、拉削過程中產生振動。消除拉削缺陷,提高拉削表面質量的途徑:1)提高刀齒刃磨質量,防止刃口微刃產生并保持刃口鋒利。
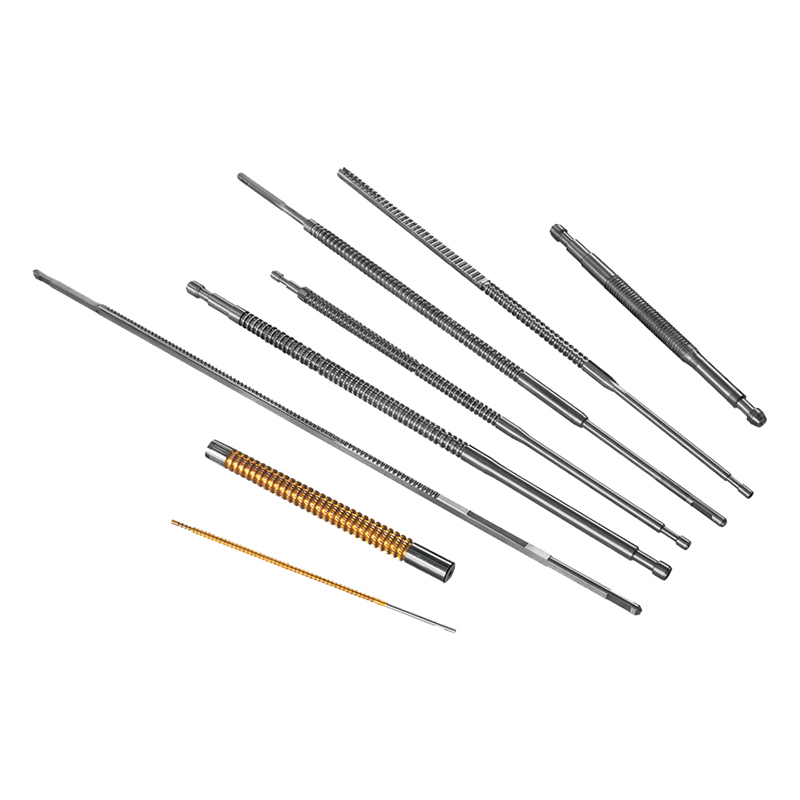
擠亮點:是由于刀齒后刀面與已加工表面間產生較劇烈的擠壓摩擦而造成的。常用選擇合適的后角(尤其是粗切齒的后角不應太?。┖妄X升量;采用性能良好的切削液,并需澆注充足,以及采取對硬度高的工件進行適當?shù)臒崽幚硪越档推溆捕鹊确椒▉硐@種缺陷。拉削后的表面上還會產生一些其它缺陷。環(huán)狀波紋:其主要原因是拉削過程中切削力變化較大,拉刀工作不平穩(wěn),使刀齒在圓周方向切削不均勻所致。