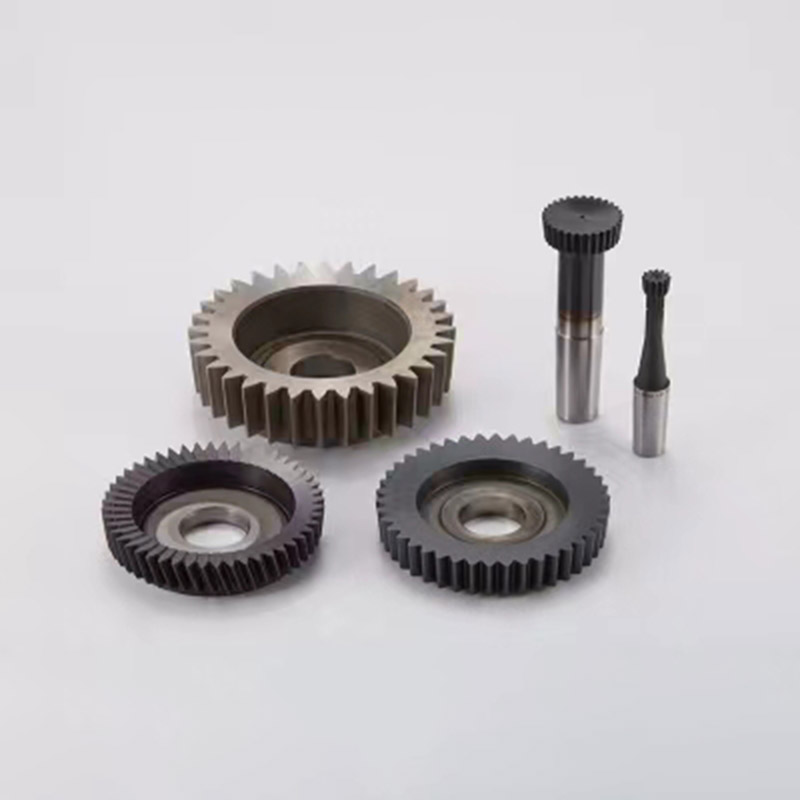
防止拉刀的斷裂即刀齒損壞:拉削時由于刀齒上受力過大,拉刀強(qiáng)度不夠,是損壞拉刀的主要原因。造成刀齒受力過大的因素:拉刀齒升量過大、拉刀彎曲、切削刃各點(diǎn)拉削余量不均勻、刀齒徑向圓跳動大、預(yù)制孔太粗糙、材料內(nèi)部有硬質(zhì)點(diǎn)、工件強(qiáng)度過高、嚴(yán)重粘屑和容屑槽擠塞以及工件夾持偏斜等。1)要求預(yù)制孔精度IT10~IT8、表面粗糙度Ra≤5μm,預(yù)制孔與定位端面垂直度偏差不超過0.05mm。2)嚴(yán)格檢查拉刀的制造精度。3)拉削高性能和難加工材料,可選取適當(dāng)熱處理改善材料? 的加工性,也常使用高性能材料的拉刀或涂層拉刀。4)保管、運(yùn)輸拉刀時,防止拉刀彎曲變形和破壞刀齒。
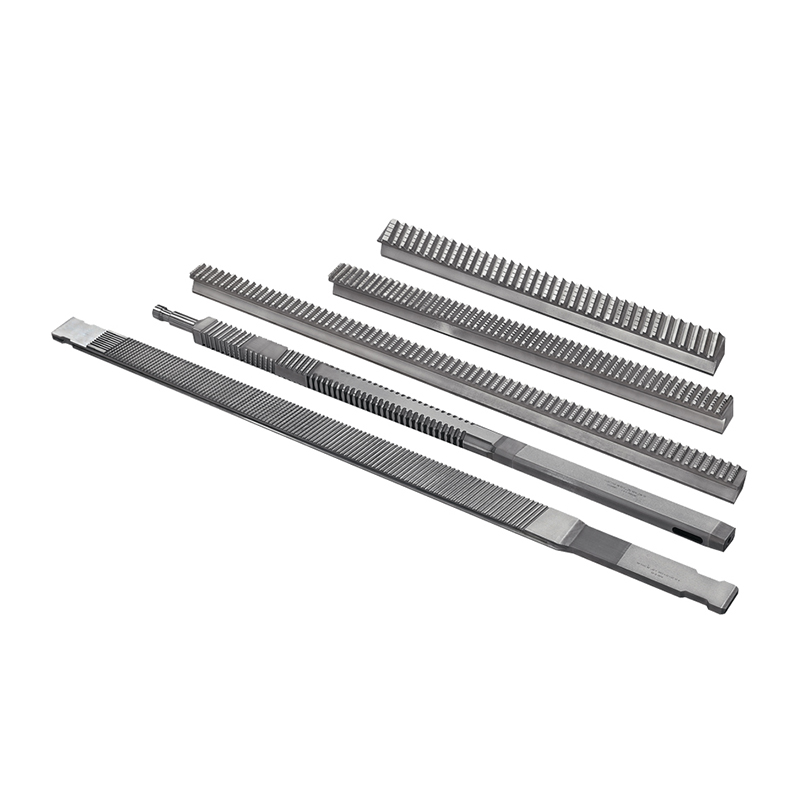
拉刀的設(shè)計特點(diǎn):加工具有復(fù)雜廓形的外表面時,通常將拉刀設(shè)計為組合式,行將若干把拉刀安裝在1個刀體上,使其分別加工同1零件的各部份表面。組合拉刀中的各把拉刀既可同時工作也可順次工作。設(shè)計組合拉刀時,首先需將待加工表面廓形劃分成若干簡單的單元。為使加工每單元的拉刀設(shè)計最簡化,同時又能提高拉削效力和縮短拉刀長度,在廓形分段及拉刀配置時應(yīng)斟酌盡量讓幾把拉刀同時參與工作,但這樣常常會造成拉刀結(jié)構(gòu)過于復(fù)雜、拉刀及其緊固件布置困難、拉床過載、零件加工時變形過大、排屑困難等問題,因此在多數(shù)情況下采取同時加工與順次加工相結(jié)合的方式來安排拉刀位置,公道拉削復(fù)雜表面。
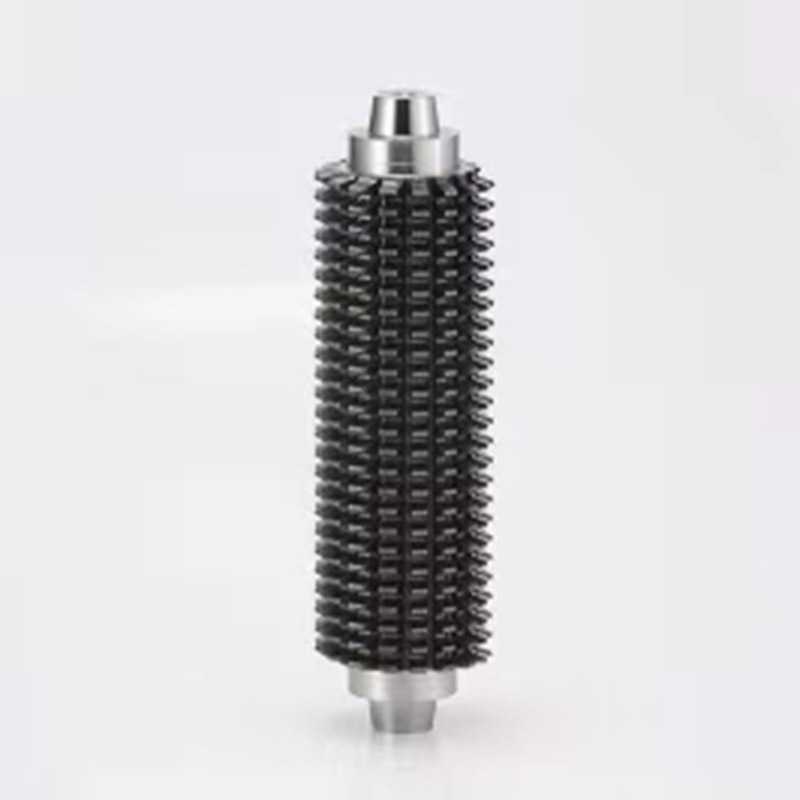
拉刀是用于拉削的成形刀具。刀具表面上有多排刀齒,各排刀齒的尺寸和形狀從切入端至切出端依次增加和變化。當(dāng)拉刀作拉削運(yùn)動時,每個刀齒就從工件上切下一定厚度的金屬,最終得到所要求的尺寸和形狀。拉刀常用于成批和大量生產(chǎn)中加工圓孔、花鍵孔、鍵槽、平面和成形表面等,生產(chǎn)率很高。拉刀按加工表面部位的不同,分為內(nèi)拉刀和外拉刀;按工作時受力方式的不同,分為拉刀和推刀。推刀常用于校準(zhǔn)熱處理后的型孔。